Understanding Pressure Vessel Testing: A Comprehensive Guide for Businesses
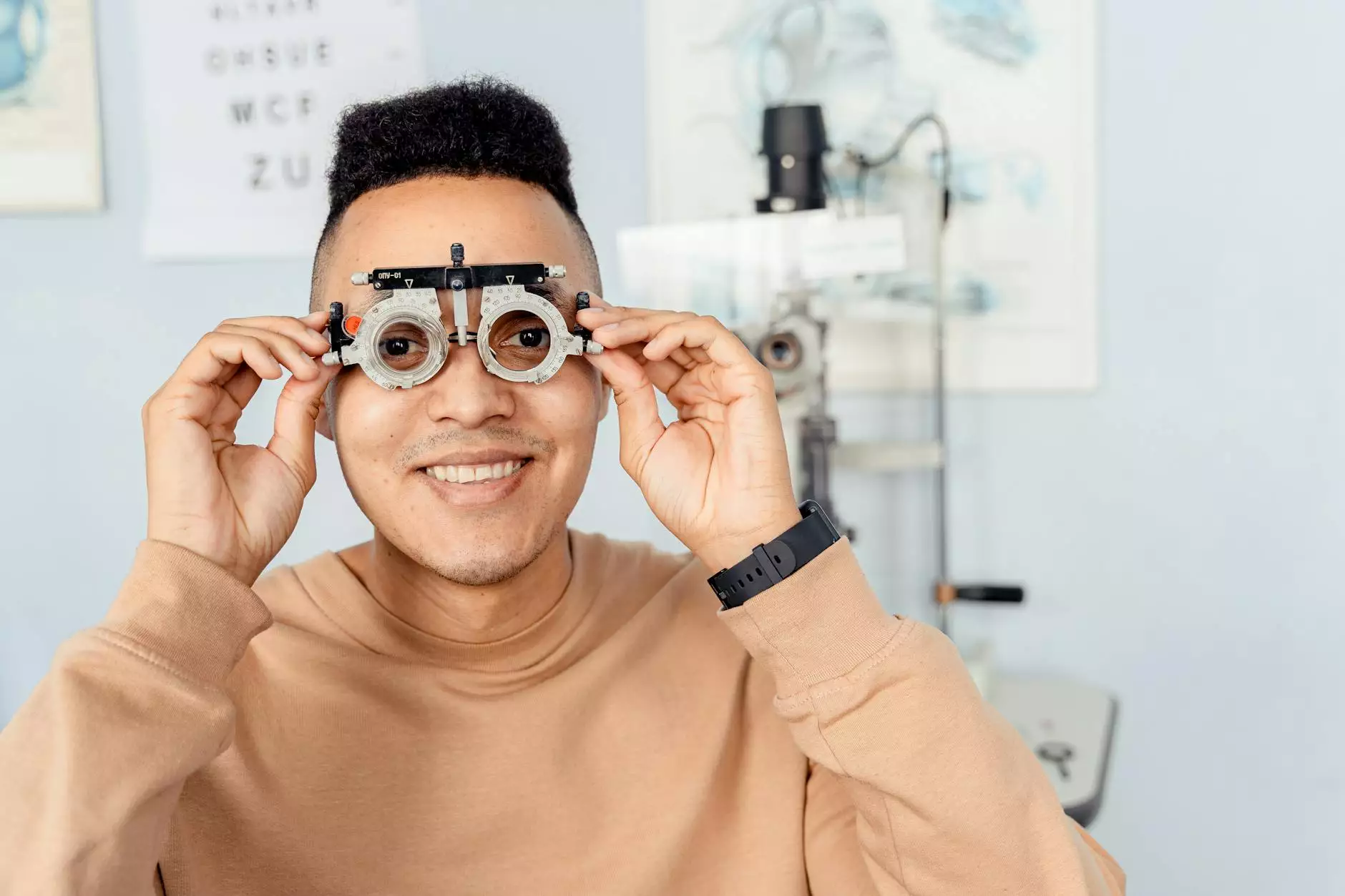
In the landscape of industrial safety, pressure vessel testing stands as a pillar of compliance and safety. For businesses, particularly in sectors such as construction, manufacturing, and energy, understanding the intricacies of pressure vessel testing is paramount. This article delves into the complexities of pressure vessel testing, its importance, methodologies, and how businesses can navigate this critical aspect effectively.
The Importance of Pressure Vessel Testing
Pressure vessels are containers designed to hold gases or liquids at a pressure substantially different from the ambient pressure. When these vessels fail, the repercussions can be catastrophic, leading to significant safety hazards, economic losses, and legal ramifications. Thus, the necessity of pressure vessel testing cannot be overstated.
- Compliance with Safety Regulations: Occupational safety regulations mandate that pressure vessels undergo rigorous testing to ensure they meet safety standards set by governing bodies.
- Preventing Failures: Regular testing helps in identifying weaknesses and preventing potential failures that could lead to dangerous situations.
- Reducing Liability: Implementing thorough testing protocols can minimize the legal liabilities associated with pressure vessel operations.
- Enhancing Operational Efficiency: A well-tested pressure vessel operates more efficiently, leading to optimized production and reduced downtime.
Types of Pressure Vessel Testing
Several testing methods are employed to ensure the structural integrity and safety of pressure vessels. Each method has its specific applications and advantages. Below are some of the most common types of pressure vessel testing:
1. Hydrostatic Testing
Hydrostatic testing is one of the most widely used methods for pressure vessel testing. This involves filling the vessel with a liquid, usually water, and pressurizing it to verify its integrity.
- Advantages: It detects leaks and identifies weak points in the vessel. It is generally seen as one of the safest testing methods.
- Disadvantages: It may not reveal weaknesses that only appear under operational conditions.
2. Pneumatic Testing
Pneumatic testing uses gas, often air, to pressurize the vessel. This method can quickly identify leaks and is used when water is not a feasible option.
- Advantages: It can be rapidly conducted and is suitable in circumstances where water usage is impractical.
- Disadvantages: Pneumatic testing carries a higher risk, as gas can expand rapidly, leading to potentially explosive outcomes.
3. Non-Destructive Testing (NDT)
NDT incorporates various methods such as ultrasonic, magnetic particle, and radiographic testing to assess the material integrity without causing damage to the vessel.
- Advantages: Ensures that the vessel remains operational post-testing and effectively reveals structural flaws.
- Disadvantages: These methods can be more expensive and require skilled operators.
4. Visual Inspection
A simple yet effective method, visual inspection involves thoroughly examining the vessel for visible signs of damage, corrosion, or wear.
- Advantages: It is cost-effective and quick, often serving as a preliminary step before more thorough testing.
- Disadvantages: It cannot detect subsurface issues and is subject to the inspector's expertise.
Regulatory Compliance and Standards
Businesses must adhere to strict regulations concerning pressure vessel testing. In the UK, the Pressure Systems Safety Regulations (PSSR) 2000 are crucial in guiding businesses on the safe operation of pressure systems. Compliance ensures not just legal safeguarding but also enhances the overall safety culture within organizations.
Key Regulations to Consider
- Health and Safety at Work Act: This act emphasizes the responsibility of employers to ensure the health and safety of their employees, which includes maintaining pressure vessels.
- Design and Manufacture Regulations: Regulations governing the design and fabrication of pressure vessels must be meticulously followed to ensure safety standards are met.
- Regular Inspection Requirements: Companies are required to establish a regular inspection and testing routine, detailing the frequency and types of tests to be performed.
Implementing an Effective Pressure Vessel Testing Program
Establishing a comprehensive pressure vessel testing program can significantly bolster safety and reliability. Here’s how businesses can implement such a program:
1. Assess Your Equipment
Begin with a thorough assessment of all pressure vessels used in your operations. Identify their specifications, operational pressures, and past inspection history. Knowing your equipment is crucial for scheduling and deciding on testing methods.
2. Develop a Testing Schedule
Creating a rigorous testing schedule ensures no vessel is overlooked. Factors influencing the frequency of testing include:
- The vessel's operating conditions.
- Historical performance data and previous test results.
- The potential consequences of failure.
3. Choose the Right Testing Methods
Select appropriate testing methods based on the type of pressure vessel, its usage, and regulatory requirements. A combination of methods may yield the best results to ensure comprehensive safety.
4. Train Your Staff
It’s essential that employees involved in operating and maintaining pressure vessels receive adequate training. Understanding both the operational mechanics and safety protocols will reduce human error and enhance safety awareness.
5. Document Everything
Maintain meticulous records of all testing procedures, results, and inspections. Documentation is not only crucial for regulatory compliance but also for continuous monitoring and maintenance.
Conclusion
In today's industrial landscape, prioritizing pressure vessel testing is not just an operational necessity but a moral obligation. The safety of employees, the environment, and the public must never be compromised. By understanding the importance of testing, implementing a rigorous testing program, and adhering to relevant regulations, businesses can safeguard their operations and positively impact their bottom line.
For more information on pressure vessel testing and related services, visit Safe Plant UK. Elevate your business’s safety standards to ensure compliance and foster a secure working environment.